Cutting Through Time: The Evolution of Water Jet Technology to 2025
A Stream of Innovation: Water Jet Cutting from Origins to 2025
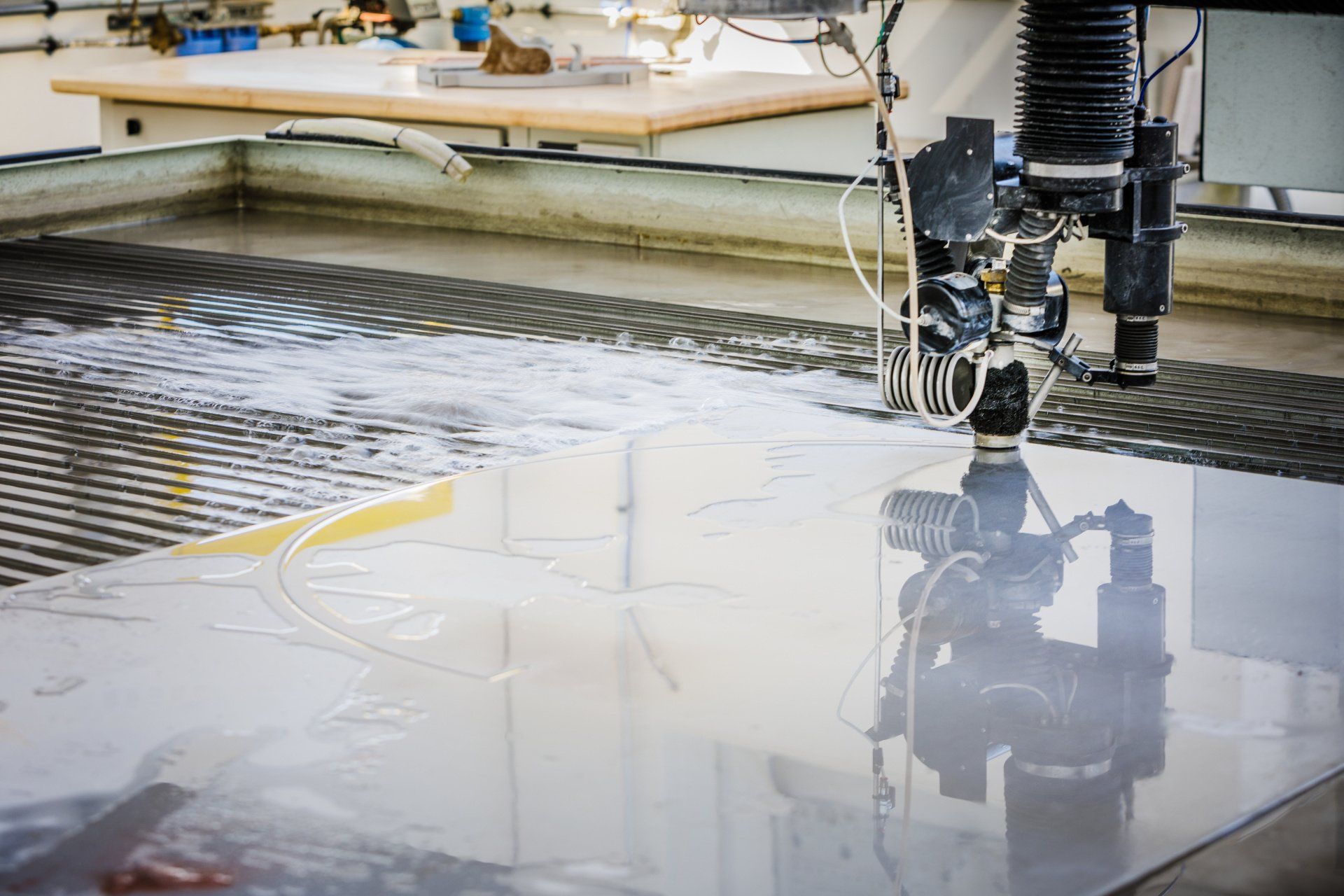
Precision Under Pressure: The Technical Evolution of Water Jet Cutting (1850–2025)
Water jet cutting has become an essential process in modern manufacturing, known for its ability to slice through nearly any material with high precision and without introducing heat-affected zones. From rudimentary hydraulic mining systems to AI-optimized cutting platforms, this blog explores the technical milestones, performance metrics, and market growth of water jet cutting over the past 175 years—culminating in the smart, sustainable machines of 2025.
🧱 1850s–1950s: From Erosion to Engineering
Water erosion was humanity’s first exposure to the power of high-pressure flow. In the mid-19th century, hydraulic mining used pressurized water (typically under 800–1,000 psi) to move earth and uncover gold deposits in the western U.S.
The transition to industrial applications began in the 1930s–1950s:
- 1937: Early high-pressure water jets (up to 10,000 psi) used for cleaning and descaling.
- 1956: Dr. Norman Franz developed a prototype capable of cutting soft materials like plywood with water jets at pressures exceeding 40,000 psi—an innovation laying the groundwork for precision water jet cutting.
🛠️ 1970s: Commercial Systems and Pure Water Cutting
The first commercially viable water jet systems emerged in the 1970s, with companies like Flow Industries developing machines for soft material cutting.
Key Technical Specs (1970s Systems):
- Max pressure: ~30,000–40,000 psi
- Nozzle diameter: 0.010–0.020 inches
- Materials cut: Paper, plastic, foam, cardboard
- Accuracy: ±0.01–0.05 inches
Though limited to non-metallics, these systems offered burr-free, dust-free cutting and clean edges without tool wear.
🧪 1980s: The Abrasive Revolution
The development of abrasive water jet (AWJ) technology in the early 1980s enabled the cutting of metals, stone, glass, and ceramics.
Abrasive Jet Enhancements:
- Garnet particles (80 mesh) introduced into water stream
- Cutting pressures reached 60,000+ psi
- Kerf width reduced to as low as
0.030 inches
- Tolerances improved to
±0.005 inches
This innovation opened the door to aerospace, defense, and tool & die manufacturing applications. By the late 1980s, abrasive jets could cut stainless steel up to 6 inches thick with smooth edges and no heat distortion.
📈 1990s–2000s: Automation, CNC, and Speed Gains
With the integration of CNC systems and better pump technology, water jet cutting evolved rapidly during the late 20th century:
Feature 1990s 2000s
Max Pressure 60,000 psi 87,000 psi
Cutting Speed (1" steel) 10 IPM 40+ IPM
Accuracy ±0.005" ±0.001–0.003"
Software G-code / CAM Full CAD-CAM Integration
Direct-drive pumps and intensifier pumps improved reliability and efficiency. The ability to program complex shapes made water jets ideal for custom fabrication and prototype development.
🌐 2010–2020: Mainstream Adoption & Environmental Benefits
By 2020, water jet systems were standard across industries such as:
- Aerospace (titanium, Inconel)
- Automotive (carbon fiber composites)
- Architecture (glass, stone inlays)
- Electronics (circuit boards)
Industry Stats by 2020:
- Market size: $1.1 billion globally
- Average system cost: $100k–$350k
- Typical ROI: <2 years
- Abrasive use: ~1 lb/minute (cost: ~$0.25–$0.40/lb)
- Water use: 0.5–1.5 gallons/minute (recyclable up to 90%)
Environmental factors like cold cutting, zero emissions, and minimal waste made water jets a preferred choice over plasma and laser in many applications.
🤖 2020–2025: Intelligence and Integration
Water jet cutting between 2020 and 2025 underwent a digital transformation:
Key Innovations:
- AI-Driven Nesting: Reduced material waste by 10–15%
- Predictive Maintenance: 20–30% less downtime through machine learning diagnostics
- Pressure Modulation: Adaptive control based on material thickness
- Closed-loop Water Systems: Up to
95% water reuse using advanced filtration
- Cloud-Based Monitoring: Real-time analytics and remote diagnostics
New Benchmarks:
- Max pressure: 90,000+ psi (6,200 bar)
- Accuracy: ±0.001 inch (25 microns)
- 3D cutting heads: 5-axis capability with ±0.5° angular accuracy
Hybrid platforms also emerged, combining water jet heads with laser or plasma to handle diverse part requirements in a single machine.
📊 Water Jet Market Outlook (2025 and Beyond)
As of 2025, the global water jet cutting market is projected to surpass $1.8 billion, driven by:
- Growth in aerospace and renewable energy manufacturing
- Increased demand for sustainable, zero-heat cutting
- Ongoing adoption of Industry 4.0 and smart factory systems
🧩 Conclusion
From gold mining to precision aerospace parts, water jet cutting has evolved into a high-tech, environmentally friendly process. It’s no longer just about cutting—it’s about control, intelligence, and integration. As pressures climb and tolerances tighten, the role of water in modern manufacturing is more relevant than ever.